Schritt 2
Die eingescannten Bilder des Spielfelds wurden im nächsten Schritt digital nachbearbeitet und vektorisiert. Dieser Prozess war notwendig, um präzise, skalierbare Datenformate zu erzeugen, die sowohl für die CNC-Fräse als auch für die Druckerei geeignet sind. Die Vektordateien ermöglichten es, exakte Konturen, Bohrungen und Designelemente des Spielfelds nachzuvollziehen und für den weiteren Produktionsprozess zu verwenden – etwa für das Fräsen neuer Bauteile oder den passgenauen UV-Druck.
.dfx Vorlage für VCarve Pro

Vektorgrafik für die Druckerei, mit Pantone Farbencodes
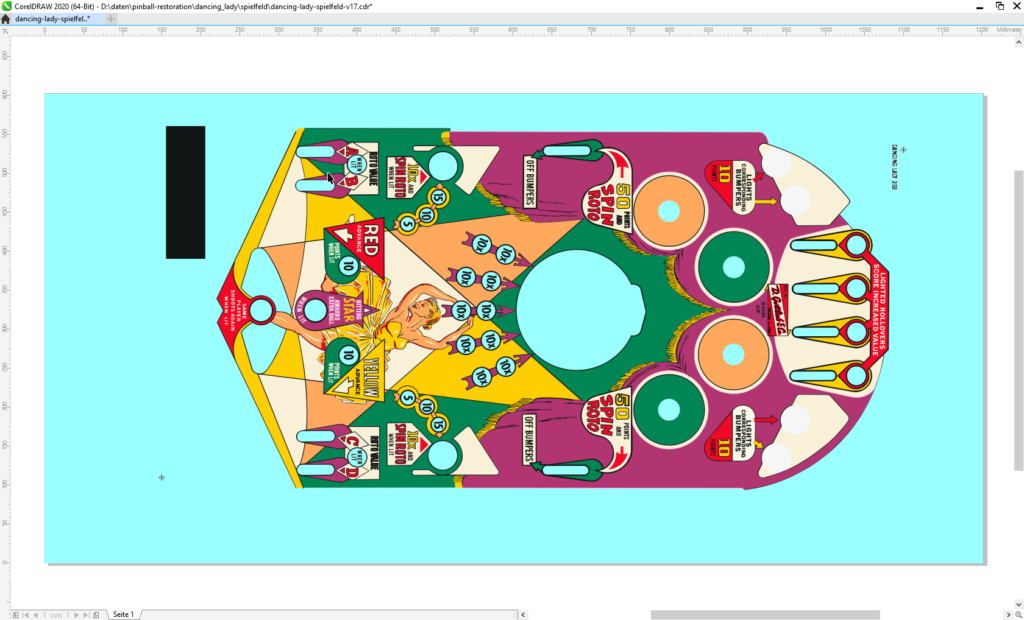
Schritt 3
Das Fräsen des neuen Spielfelds erfolgte im Happylab mithilfe einer CNC-Fräse. Als Material diente eine 15mm 1200 × 600 mm große Birke-Multiplexplatte, die aufgrund ihrer Stabilität und feinen Oberfläche besonders gut für präzise Fräsarbeiten geeignet ist. Auf Basis der zuvor vektorisierten Daten konnten alle notwendigen Konturen, Ausschnitte und Bohrungen exakt aus der Platte gefräst werden. So entstand ein passgenaues Rohspielfeld, das die Grundlage für den späteren Druck und den Zusammenbau bildete.
Schritt 4
Die Inserts – also die lichtdurchlässigen Kunststoffelemente des Spielfelds – wurden mithilfe der CAD-Software Fusion 360 digital konstruiert. Dabei galt es, sowohl die exakten Maße als auch die Positionen und Funktionen der einzelnen Teile präzise zu berücksichtigen, um eine perfekte Passform auf dem Spielfeld zu gewährleisten. Nach Abschluss der 3D-Konstruktion wurden die Modelle für den 3D-Druck vorbereitet und anschließend auf einem SLA-3D-Drucker (Stereolithografie) gefertigt. Dieses Druckverfahren ermöglicht besonders feine Details und glatte Oberflächen – ideal für durchscheinende Bauteile wie Inserts, die später Teil der Lichtshow des Flippers sind.
Schritt 5
Nachdem die Inserts gefertigt worden waren, wurden sie sorgfältig mit Holzleim auf das Spielfeld aufgeklebt. Dabei wurde darauf geachtet, dass sie genau an den richtigen Stellen sitzen, damit das Licht später gut durchscheinen kann und alles stabil bleibt. Direkt danach wurde das Spielfeld mit einem robusten 2K-Klarlack lackiert. Diese erste Lackschicht schützt die Teile und sorgt dafür, dass die Oberfläche glatt und widerstandsfähig bleibt.
Schritt 6
Der Druck wurde mithilfe eines großformatigen UV-Druckers durchgeführt. Dieses Druckverfahren ermöglicht es, die Motive direkt und präzise auf das Spielfeldmaterial aufzubringen. Dabei werden UV-Lichtstrahlen verwendet, um die Druckfarben sofort auszuhärten, was zu besonders scharfen und widerstandsfähigen Ergebnissen führt. Dank des großformatigen Druckers konnten auch großflächige Designs ohne Unterbrechungen oder Farbabweichungen realisiert werden, was die Qualität und Detailtreue des Spielfelds erheblich verbessert.
Schritt 7
Nach dem Druck erfolgte die Versiegelung des Spielfelds mit zwei Schichten 2K-Klarlack. Zwischen den beiden Lackiergängen wurde das Spielfeld sorgfältig zwischengeschliffen, um Unebenheiten zu entfernen und eine besonders glatte Oberfläche zu erzielen. Dieses Vorgehen sorgt für eine langlebige Schutzschicht, die das Design vor Kratzern und Abnutzung schützt und gleichzeitig die Farbtiefe sowie die Brillanz des Drucks verstärkt.